サイエンスソリューション部 茂木 春樹
はじめに
民間製造業の設計・開発時、製造工程検討時などに、コンピュータによるシミュレーションを活用してエンジニアリングを支援することをCAE(Computer Aided Engineering)と呼ぶが、これまで専門家が担ってきたシミュレーションを設計者自身が行ういわゆる「設計者CAE」の導入、拡大の動きが近年あらためて拡大している。しかしながら、設計者がCAEを活用する際に生じる課題も未だに耳にする機会が多い。
本コラムでは、民間製造業のお客さまに対してシミュレータの導入・活用方法構築支援を行ってきた当社の視点から、設計者CAEについて考えてみたい。
身近になった設計者CAE
「設計者CAE」の話題に移る前に、技術者の方には釈迦に説法となるが設計や開発とはどのようなものなのか、から述べていこう。
CAEがなかった頃、もしくはCAEを活用しない設計では、まず製品企画に基づき類似する既存製品や設計者の経験、アイディアなどをベースとして概念設計を行う。次に概念設計に基づき工学的な設計計算から安全率を考慮して詳細な形状寸法や材料、作動条件などを決める詳細設計を行い、試作品をつくる。試作品ができたら性能や耐久性などの試験を行って設計の妥当性を確認、問題があれば原因を特定し設計を変更、これを製品としての要件を満たすまで繰り返すことで、最終的には製品の図面として出図する。つまり、製品によって程度の差こそあれ、設計や開発には段階が存在し、その段階の間で手戻りの繰り返しが必要となる。しかも、試作に高額な費用がかかる場合(*1)、何度も試作を繰り返すことができないため、最適な設計ができないこともあるなど、設計者は多くの悩みを抱えてしまうであろうことは想像に難くない。
このような設計や開発にかかる様々なコスト(時間、費用、工数、など)の削減や設計品質の向上(最適な設計)を図るために、設計の妥当性をコンピュータ上で仮想的に検証できるCAEを設計者自身が活用していく流れは、ある意味必然であった側面もあるだろう。実際に、設計者向けの簡単に扱えるCAEソフトが発売されたり、設計者に馴染みの深い3次元CAD(Computer Aided Design)ソフトに対して拡張パッケージを導入し、CADソフトの画面からシミュレーションを簡単に実行できるようになったりと、設計者にとってCAEは身近なものになりつつある。
本コラムでは、設計者CAEを志向したソフトウェアやサービスについての詳細な動向は割愛するが、それらは年を追う毎に高機能化していることは確かであり、簡単な解析であれば少なくとも大外れはしないシミュレーション結果が得られるようになってきている。しかしながら、少し難しい解析(*2)や実際に設計へCAEを適用していくとなると、まだ設計開発現場の技術者からは解決すべき課題やハードルを数多く耳にする。
身近になってもハードルがある設計者CAE ―設計者CAEの本質的な課題―
- 望み通りの評価を実現する方法がわからない(ソフト、手法、条件、など)
- 操作や計算に時間がかかったり、エラーが頻発したりする
- 運用方法確立に時間がかかる(月単位、年単位の期間を要する場合も)
- ソフトの操作は覚えても、正しい解析結果なのか不安(理論、解析に明るくない)
- 実験事実と解析結果に大きな乖離があり、設計に活用できない、など
これらは、筆者が民間企業の設計者から直接聞いたことのあるCAEの課題を抽象化したものである。細かい話を挙げていけばキリがないが、課題の大部分は“コスト”と“結果への不安”に集約されるだろう。
まずCAEにかかる“コスト”としては、コンピュータ上でシミュレーションを行うことから、シミュレーションを実行する計算機、ソフトなどの環境整備に必要なコストだけでなく、人的コストの大きさにかかる課題も大きいようだ。例えば、シミュレーションで設計開発に活用できる結果を出そうとすると、ソフトウェアの使い方を覚える期間や結果の妥当性を検証し、運用方法を確立する期間がかかる。また、運用方法が確立しても、場合によってはメッシュの作成や計算のエラー対応など、設計の本質には関係がない作業が一定の負荷としてかかってくる。これらは、設計者から場合によっては月単位、年単位の工数を奪いかねず、環境整備とは比べ物にならないコストがかかってしまうことがある。
次に“結果への不安”については、シミュレーションの結果に対するV&V(Verification & Validation)に関連して2種類存在する。CAEにおいて重要な役割を果たすシミュレーションは、従来その専門家が担当してきており、シミュレーションが正しく実行できているかについての判断(Verification)には専門的な知識が必要となる。もうひとつは、現実との比較検証(Validation)、すなわちシミュレーションの“確からしさ”であり、設計者の視点からは最も大きな不安である。設計開発の効率化や品質向上を目的としてCAEの適用を試みたのに、シミュレーションの結果が活用できないほど実験結果などから乖離があっては目的を果たすことはできない。
“結果への不安”は、“コスト”をかければ解決できる側面があるものの、設計者自身で両者のバランスを取ることは非常に難しい。言い換えれば、設計者自身が“コスト”をかけてまで“結果への不安”を解消することが難しい、ということが本質的な課題と言えるだろう。
本当に“使える”設計者CAEとは
それでは上記課題を解決し、本当に“使える”設計者CAEは存在するのであろうか。また、それはどのようなものである(べき)だろうか。答えは人によって異なるはずだ。そもそも対象の素性に応じてCAEに要求される技術水準は異なるだろうし、同じ製品を取り扱う企業であっても、各社で設計開発のやり方が異なる場合もあることなどから、本当に“使える”設計者CAEの姿は様々想定される。
しかし、少なくともCAEの目的はシミュレーションを行うことではなく、シミュレーションから得られる結果を活用してより良い設計を目指すことである、という点は誰もが納得するところではないだろうか。この観点から考えると、設計者CAEは設計の段階や目的に応じて適切な姿が異なることになる。
ここで、設計や開発における段階とCAEの関係について、シミュレーションにかかる様々な“コスト”を縦軸に、シミュレーション結果の“確からしさ”を横軸にとって整理した図を示す。
図:設計開発の段階に応じて要求されるCAEのイメージ
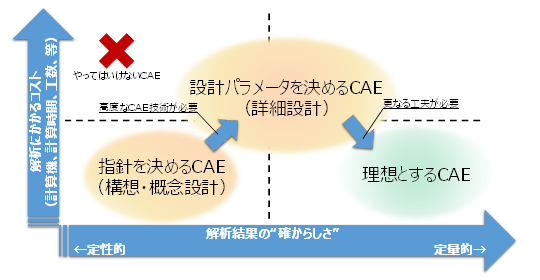
製品や企業によって細かい設計の進め方は異なっても、構想段階から詳細な設計に落とし込んでいく大きな2段階は変わらないだろう。これに対応して、CAEも2段階存在すると言える。設計の構想段階においては、設計者の経験やアイディアに基づく設計の妥当性を確認し、方向性を定めることが重要となる。そうであれば、シミュレーションに過度なコストをかけることは不要であるし、結果も定性的に妥当であれば問題ない。これに対し詳細設計の段階においては、詳細なパラメータ(形状寸法、材料、作動条件、など)を決め、その妥当性を検証することが重要となるので、多少コストはかかってもより“確からしい”結果を出せるシミュレーションが必要となってくる。
後者には高い技術水準が要求される場合もあるが、シミュレーションへの専門的な知識がない設計者でも、人的コストがかからない状態で取り扱うことができるようになっている必要があるだろう。また、究極的にはシミュレーションにかかる様々なコストが低く、解析結果も確からしいものが“理想的なCAE”であると言える。
以上より、非常に抽象的な表現となってしまうが、本当に“使える”設計者CAEとは、設計の段階に応じて適切なシミュレーション技術を、運用方法まで確立済の状態で、設計者が大きな工数をかけることなく使用可能なもの、であると言えるだろう。設計者CAEを志向した商用ソフトウェアは前述の通り高機能化が進んでいるものの、運用方法の確立や設計者の工数を考慮すると不十分な点もあり、今後もしばらくはその状態が続くものと推測される。
最後に
当社では、「シミュレーションを設計開発に活用する」ことを目的として、設計の本質とは関係がないメッシュ生成、各種設定(モデル設定、数値解法、境界条件、など)をお客さまの解析対象に最適化し、可能な限り自動化した設計者向けの専用解析システムを提供してきた実績を有している。また、対象とする分野は限定されるが、ソフトウェア導入後すぐに設計開発で活用できることをコンセプトに、解析の“確からしさ”を確認するために必要な実測を含めた、実験との比較検証に関するコンサルテーションも行っている。
特に、まだ設計者には取り扱いにくい、複数の物理現象が様々なスケールで複雑に影響し合ういわゆるマルチスケール‐マルチフィジックスな対象であっても、シミュレーションの精度を担保しながら高速に実行するための技術、ノウハウも蓄積してきており、「理想とするCAE」を一部実現しつつある。
当社は今後も民間製造業のお客さまが抱える課題の解決を通じて、単なるソフトウェアの提供だけではなく、お客さまの解析対象や背景にある現象を深く理解し、本当に“使える”CAEとは何か?を常に考える姿勢を維持して、より高度なCAEを設計者が“使える”よう少しでも貢献していきたい。
注釈
- *1)たとえば試作に金型が必要な場合、1つの金型あたり数百万円以上かかる場合もある。
- *2)ここでは構造解析では弾塑性解析、接触解析、流体解析では乱流解析、二相流解析、などのほかに、複数の物理現象が関係するマルチフィジックス解析も含む。
関連情報
-
専用シミュレーションシステムの構築
-
製造業向けデジタルエンジニアリング関連ソリューション