みずほ情報総研 経営・ITコンサルティング部 主席コンサルタント 岩崎 拓也
- *
本稿は、『カレントひろしま』2018年11月号(発行:一般財団法人ひろぎん経済研究所)に掲載されたものを、同編集部の承諾のもと掲載しております。
はじめに
本稿では3Dプリンティングの概要について概観した後、現状の動向や活用に向けた取り組み等について述べる。3Dプリンタが世界中でブームになっている一方で、日本においては活用が幾分遅れているのが現状ではないだろうか。その理由の1つは3Dプリンタの“夢”が語られることは多いが、3Dプリンティングの様々な手法やその特徴、課題などがあまり伝えられていないためではないかと筆者は考えている。
3Dプリンティングは“何でもできそうで何もできない”ものではない。何をやりたいかが明確になれば、従来ではできなかったものが作製できるようになり、技術革新に繋がる可能性を秘めているものである。本稿を通じて、多くの方が3Dプリンティングをよりよく理解し、今後の活用促進の一助になれば幸いである。
3Dプリンティングとは
1.1. Additive Manufacturing(AM)
“3Dプリンタ”という言葉は一般にも広く周知されてきており、一般の方でも何度も耳にしたことがあるのではないだろうか。では、“Additive Manufacturing”という言葉はどうであろう。略して単に“AM”と呼ばれることも多い。過去には“Rapid Fabrication”など様々な呼び方がされていたが、2009年にASTM InternationalのInternational Committee F42において“Additive Manufacturing”という用語が正式に定義された。材料を基板や他の材料に積み重ねていく製造方法というニュアンスがよく伝わる言葉である。
一般に“3Dプリンタ”は樹脂系の材料を使う比較的低価格の装置を指す際に使われることが多く、高精度でハイエンドな産業向け装置まで含めた場合には付加製造装置(AM装置)と呼ばれているようである。以降、本稿ではAMという用語を利用することとする。
1.2. AM技術の7つの分類
ASTMではAM技術を7つに分類している。図表1に7つの方式の概要を示す。1990年代に産業界での利用が広がった光造形は液槽光重合(Vat Photopolymerization)に分類される。2013年以降、日本においても家電量販店等で一般向けとして販売されたAM装置は材料押出(Material Extrusion)に分類されるものであり、FDM(Fused Deposition Modeling、熱溶解積層法)の名称が使われることも多い。産業用の高精度なFDM装置も各種販売されている。鋳造用砂型の造形等に利用されているのは結合剤噴射方式(Binder Jetting)、カラーで高精細な樹脂造形が可能なタイプは材料噴射方式(Material Jetting)、微細な金属や樹脂の粉末をレーザーや電子ビーム照射で溶融させながら高精細な造形が可能なものは粉末床溶融結合方式(Powder Bed Fusion)である。金属部品の補修を行うなど金属粉末を吹きつけながらレーザー等で溶融させるタイプは指向性エネルギー堆積方式(Directed Energy Deposition)である。それぞれの方式ごとに得意な材料や造形物の精度等が異なるので、目的に応じて適切な方式の装置を選択することが重要である。
図表1 AM技術の7つの分類と代表的な装置メーカー
左右スクロールで表全体を閲覧できます
造形方式 | 概要 | 代表的な材料 | 代表的な装置メーカー |
---|---|---|---|
シート積層 |
シート状の材料を層ごとにレーザーやカッターで切断しながら積み重ねていく積層造形方法 |
紙、樹脂、金属 |
Mcor Technologies(アイルランド)、Fabrisonic(米国) |
液槽光重合 |
液槽に溜めた光硬化性樹脂をレーザー等により部分的に選択、硬化させ積層する造形方法 |
光硬化性樹脂、セラミック |
3D Systems(米国)、シーメット(日本) |
材料押出 |
加熱することにより溶融状態になる樹脂をノズルより押し出し積層させる造形方法 |
熱可塑性樹脂(金属粉混合材料含む) |
Stratasys(米国)、3D Systems(米国)、XYZ Printing(台湾)、Desktop Metal(米国) |
結合剤噴射 |
液状の結合剤(バインダー)をノズルより噴射し、粉末材料を結合させる積層造形方法 |
樹脂、金属、砂、石膏、セラミック |
3D Systems(米国)、ExOne(米国)、Voxeljet(ドイツ)、HP(米国)、TRAFAM(日本) |
材料噴射 |
液体材料をノズルより噴射し、選択的に堆積させていく積層造形方法 |
光硬化性樹脂、ワックス |
Stratasys(米国)、3D Systems(米国)、ディーメック(日本)、キーエンス(日本) |
粉末床溶融結合 |
粉末材料の特定領域をレーザーや電子ビームの熱エネルギーにより選択的に溶融・結合させる積層造形方法 |
金属、樹脂、セラミック |
Arcam(スウェーデン:現、GE Additive)、3D Systems(米国)、EOS(ドイツ)、SLM Solutions( ドイツ) 、ConceptLaser(ドイツ:現、GE Additive)、Realizer(ドイツ:現、DMG森精機)、Renishaw(イギリス)、アスペクト(日本)、松浦機械製作所(日本)、ソディック(日本)、TRAFAM(日本) |
指向性エネルギー堆積 |
金属材料を供給しながらレーザー等で熱エネルギーを与え、溶融・堆積させる造形方式 |
金属 |
Optomec(米国)、TRUMPF(ドイツ)、DMG森精機(日本)、ヤマザキマザック(日本)、TRAFAM(日本) |
(注) 全ての装置メーカーが掲載されているわけではない
(出所) 各種公開情報をもとにみずほ情報総研作成
1.3. AMが世界中で注目され始めるまで
本節では、AMが何故これ程までに注目されるようになったのか、主として知的財産の観点から述べる(図表2参照)。
世界で最初にAM装置が発明されたのは1980年、名古屋市工業研究所の小玉秀男氏による光造形装置である。残念ながら当該技術の特許は1984年に米国Chuck Hull氏が取得し3D Systems社を創業、現在に至っている。樹脂向け粉末床溶融結合方式に使われている粉末焼結造形法(SLS、Selective Laser Sintering)やFDMの特許も80年代に出願されている。AMの歴史の転機となったのは2009年に米国Stratasys社が保有していたFDMの基本特許が切れたことであろう。それまでは産業用の高価な装置しかなかったが、特許が切れたことでFDMのオープンソース開発が進み多数の企業が参入してきた。その結果、装置価格は数十万円から数万円にまで低下し、企業のみならず個人でも利用可能となった。この頃から個人によるものづくりの機運が高まり、Fablabとも呼ばれる街中でのものづくり工房も広まりだした。
こうしたなか、米国のChris Andersonが著書「MAKERS」を発表し、「3Dプリンタにより個人がものづくりの主役(製造者)になれる」、「新たな産業革命が起きる」との論を展開、さらに2013年2月には米国オバマ大統領が一般教書演説において3Dプリンタに言及し、「3Dプリンタに代表される技術によって製造分野でイノベーションを起こす」と述べ、米国の競争力強化のための戦略分野に位置づけたことで世界中でAMが認識され、大ブームに繋がっていった。
AMブームの契機となったのはFDMの基本特許が切れたことであったが、2014年にはSLSの基本特許が切れた点も注目すべきであろう。FDM特許が切れた4~5年後には低価格帯の様々な装置が世界に広まった。SLSは樹脂向けの粉末床溶融結合方式の装置であり、既に10分の1程度の価格となった装置も世の中に出回りだしている。SLS装置はFDMよりも高精度な造形が可能であり(但し、FDMよりも一般的にコストは高くなる)、今後の産業分野への普及動向は注目しておくべきであろう。
図表2 AMがブームとなった歴史的背景
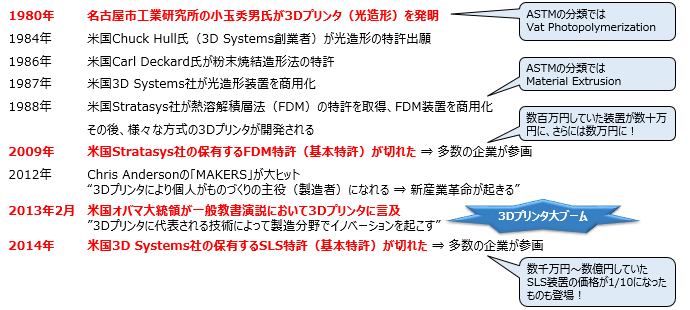
(出所)各種資料をもとにみずほ情報総研作成