みずほリサーチ&テクノロジーズ 環境エネルギー第2部 谷口 友莉
- *本稿は、『産業洗浄』No.28(日本産業洗浄協議会、2021年11月発行)に掲載されたものを、同編集部の承諾のもと掲載しております。
国内のプラスチックリサイクルの状況
使用済製品などの廃プラスチックを回収し、再資源化(リサイクル)しようという方針は国が掲げ、産業界も賛同してビジネスチャンスを捉えようという段階である。一方で、足元の状況を見ると、2019年の日本国内の廃プラスチック排出量850万トンの処理割合は、マテリアルリサイクル(再生利用)が22%(186万トン)、ケミカルリサイクル(高炉・コークス炉・ガス化(化学原料))は3%(27万トン)、サーマルリカバリーもしくは未利用が残りの75%を占める(図1)。
国内で排出される廃プラスチックの3/4が焼却され、再生材とはなっていない状況である。
廃プラスチックを再生材に戻すリサイクルは、マテリアルリサイクルとケミカルリサイクルに大別される(表3)。生産・加工品ロスなど、単一素材で樹脂の種類が明確なもの、例えば使用済PETボトルやPSトレーなどについては国内でもマテリアルリサイクルが行われている。例えば、飲料メーカーによるPETボトルのボトルtoボトルリサイクルの他、家電メーカーでも自社製の使用済製品のプラスチック樹脂を新しい製品の材料に戻す技術が実用化されている。
ケミカルリサイクルによる廃プラスチックの処理量は少なく、また国内処理量の大半は製鉄業でのコークス炉化学原料化もしくは高炉還元である。コークス炉化学原料化については、処理量が多く実績が豊富な一方で、原料に戻る割合が40%程度と、リサイクルとしての評価が分かれる場合がある。高炉還元は廃プラスチックの焼却とほぼ同義であり、再生材は作られない。気候変動対策の面から長期的には向かい風の情勢となる可能性も高い。一方で、ケミカルリサイクルには、モノマーや油、ガスを経由してプラスチック樹脂に戻そうという各種の技術も存在し、廃プラスチックを同一品質や製品に戻すクローズドリサイクルを実現するとの期待も高まっている。
ここ数年のプラスチック問題の盛り上がりを受けて化学メーカーなどが各地で廃プラスチックの油化、ガス化、モノマー化によるケミカルリサイクル技術の実証事業を進めている。再生材の品質や対応できる廃プラスチックの範囲の広さから、特に油化やガス化が注目されているようだ。海外大手各社も実用化に向けたテストを進め、リサイクルプラントに投資するなどの報道も多い。ただ、まだまだ技術的な蓄積が少なく、さらにはエネルギーコストが大きく、巨額の設備投資が必要などの壁がある。過去には国内でも廃プラスチックのモノマー化や油化の事業を行った例もあったものの、原料となる廃プラスチックの回収量の確保、コスト、事業規模の確保が壁となって撤退した歴史もある。昨今のプラスチック問題の盛り上がりで再びリサイクル技術が進化し、国内でも事業化に向けて盛り上がったとしても、「入口」と「出口」の課題を解決しなければ、過去と同じ壁は超えられない。つまり、「入口」で大量の廃プラスチックを安定的に確保し、「出口」で生産した再生材の確実な供給先を確保する必要がある。
図1. 廃プラスチックの国内処理割合(2019年)
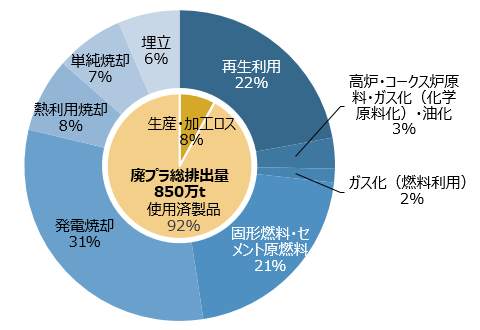
(出所)一般社団法人プラスチック循環利用協会「2019年プラスチック製品の生産・廃棄・再資源化・処理処分の状況」より作成
表3. プラスチックリサイクルの技術や事例の整理
左右スクロールで表全体を閲覧できます
リサイクル技術 | 概要・事例 | 強み・現状 | 課題 | |
---|---|---|---|---|
マテリアル リサイクル |
洗浄、破砕、成形 |
生産・加工品ロスなどの他、使用済PETボトルやPSトレーも実用化済。協栄産業、遠塚グリーンペット(PETボトル)、エフピコ(PETボトル、PSトレーなど)他。使用済家電からのプラ資源循環の例も。 |
単一素材で樹脂の種類が明確なものが対象。選別・洗浄、メカニカルリサイクル技術が進化してきた。 |
パレットや土木資材など大半の再生樹脂の用途は限られる。使用済PETボトルのリサイクル率は高いが、PE,PP,PSの国内リサイクル率は高くない。 |
ケミカル リサイクル |
モノマー化 |
PET解重合技術は国内でも実用化済。2000年代初頭に国内でも事業化したものの、廃PETボトルの輸出急増による原料不足で撤退した過去も。PSなどの実用化研究も欧米で再開;PETは日本環境設計(旧ペットリファインテクノロジー)、LoopIndustries(カナダ)、Indorma Ventures(タイ/米)など。PSは欧米のPS大手INEOS Styrolution、Trinseoなどがスタートアップと提携・共同開発中。 |
着色・汚染があっても除去しやすい。PET再生材は食品包装用途にも使用可。 |
解重合反応のために大きなエネルギー(加熱用)が必要。モノマー収率の改善も必要。PETのメカニカルリサイクルよりコスト高。 |
油化 |
熱分解油を石油精製原料やナフサクラッキング原料に加える方法が少量ながら実用化。コストや事業規模の問題で国内では過去の撤退例もあるが、再び国内の化学大手が事業化を目指す。先行する独BASFがPE,PP,PS主体の混合廃プラの熱分解油で2018年実用化テスト。SABIC、LyondellBasell、Dow、Shellなども着手。 |
混合廃プラも対象、熱分解油をナフサクラッキングすれば、PE,PP,PSのクローズドループリサイクルが可能。 |
加熱用に大きなエネルギーも必要で、熱分解反応を制御し、必要な質の熱分解油を製造することが技術的に困難(ナフサ収率向上が必要)。熱分解を阻害するため、PVC,PETの除去が必要。熱分解油製造&クラッカー設備の柔軟性・拡張のための巨額の投資や事業規模の確保が必要。 |
|
ガス化 |
実用化例が少ない。昭和電工(2003年に実用化、アンモニア製造)の他、Enerkem(カナダ)の商業プラントが2017年稼働。積水化学が実証予定(合成ガスをエタノール転換する微生物発酵技術をLanzaTechと共同開発) |
原料廃プラの適応範囲が広い。PVCやPETが入った混合廃プラや木質バイオマス、都市ごみが対象となることも。生成した合成ガスは化学品に転換可能。 |
設備費が大きく、技術的にもパイロットレベルが多い。合成ガスの用途確保が必要(燃料利用されるケースも)。再生のステップが多いため、収率向上には限界も。 |
|
ガス化 |
ケミリサでは国内廃プラ処理量が最も多い。1200℃のコークス炉で、廃プラを炭化水素油(40%)、コークス(20%)、水素やメタンなどのコークス炉ガス(40%)に転換。日本製鐵が技術開発・実用化、操業中。 |
生成した油はプラ原料に使用可能、有害物の発生が少ない。国内の処理設備余力あり。 |
生成したコークス(高炉還元剤)、ガス(燃料用)は1回使用でなくなる。 |
|
高炉還元 |
高炉でコークスの一部を廃プラで数%置き換え、還元剤として活用。JFEスチールが実用化、操業中。 |
コークスに比べてCO2発生量30%減。国内の処理設備余力あり。 |
廃プラの燃焼とほぼ同義。 |
(出所)各種資料よりみずほリサーチ&テクノロジーズ作成
関連情報
この執筆者はこちらも執筆しています
-
2021年2月1日
循環経済 ―サーキュラー・エコノミーへの波(1)
-
2020年1月
『みずほグローバルニュース』 Vol.105 (2019年10月発行)